From the first time Takara Olson laid eyes on a forge, she knew she wanted to become a blacksmith.
Now living in Nicollet, Olson grew up in Colorado and had a distinctly unique childhood. Her mother enjoyed participating in historical reenactments—particularly those based around the fur trade era and brought Olson along to the events, too. They traveled to many events throughout the year and tried to be as historically accurate as possible, living in canvas tents, wearing homemade clothes and using traditional techniques for cooking dishes and washing laundry.
When Olson was seven, she and her family attended a reenactment in the Rocky Mountains, and she came across a “really awesome” blacksmith giving demonstrations of historical trade techniques.
“He let us pump the handle on his forge to make the coals hotter,” Olson recalled. “My aunt dragged my mom over to meet this blacksmith, since we kids would not leave him alone. Thank goodness he had a lot of patience.”
Olson and her mother developed a friendship with the blacksmith, Wally Hunter, and ended up visiting him in his home state of Minnesota a few months later.
“We never left,” Olson said with a laugh. “In a way, I actually got to pick out my own dad, and he is the best dad I could ever have asked for.”
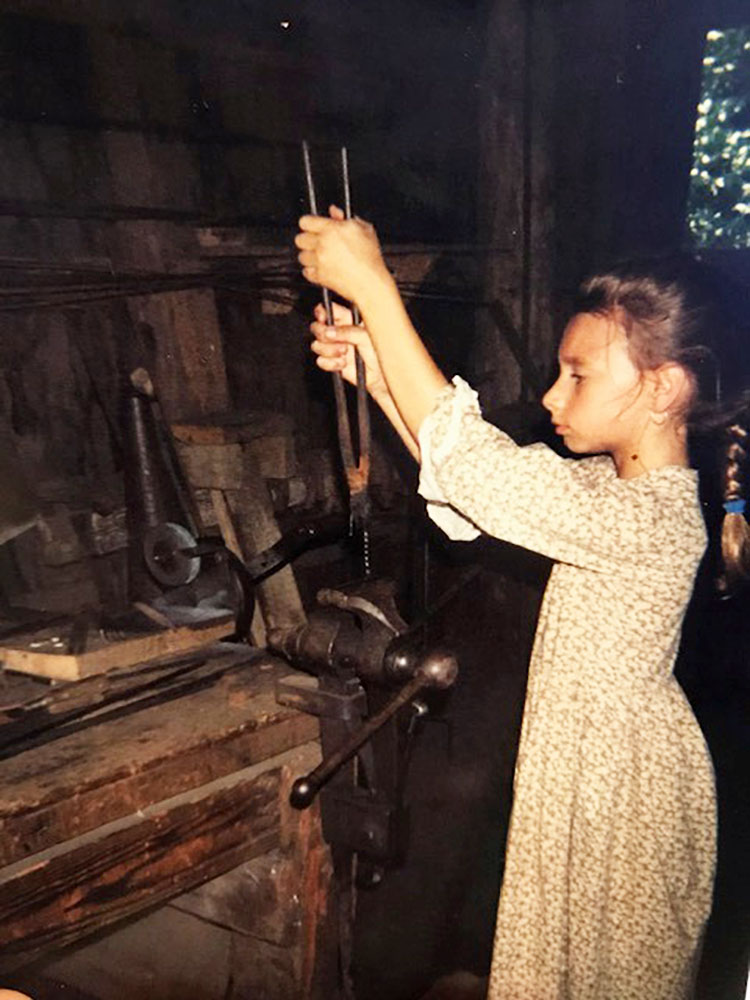
Hunter has been blacksmithing since he was in his early thirties, usually working with equipment he had inherited from his grandfather and great-grandfather. When Olson became a part of his family, she also became part of the family history and she immediately fell in love.
“Literally from the moment I met my [step]-dad, I thought blacksmithing was the coolest thing in the world,” Olson recalled. “I’ve grown up always wanting to be a blacksmith, and always learning. I love the fire; the sound of the metal being hit. It’s just kind of relaxing… and it’s a great way to take out your anger and aggression issues!”
A Learning Curve
While Olson began “tinkering around” in her father’s shop early on, she wasn’t allowed to touch any hot metal. But she was allowed to build things out of leftover metal that he didn’t need, such as the “burrs,” or rough pieces of metal that are left over after a piece is modified such as when a hammer strikes a metal’s surface.
“I was always building little coat hooks,” Olson said. “I’d take the burrs, [which] were long triangles, and I’d smooth them out and drill a hole in them, and I’d build coat hangers. They were not real pretty, but they were very functional. My parents’ house was littered with them. We keep finding them in my dad’s shop.”
By the time she was eight, Olson could recite most of the rules blacksmiths needed to know, such as what to do around a hot fire, correct pounding techniques on cold iron and which color indicated which temperature as metal was heating. Because of this, her father decided she was finally ready to heat up her first piece of metal.
I’ve grown up always wanting to be a blacksmith…. I love the fire; the sound of the metal being hit. It’s just kind of relaxing and it’s a great way to take out your anger and aggression issues!
“I did, and every rule went right out of my head,” she admitted. “I grabbed my tongs and took the metal out of the forge, and I ran to show my dad… and I tripped over my black lab and slapped myself in the face.”
Luckily, the burn wasn’t severe enough to require hospitalization; in fact, the resulting scar has almost completely faded by now. It did take some time for Olson to earn her parents’ trust in the shop again, and she said she learned a valuable lesson about safety.
“Let’s just say I’ve never been careless with metal again,” she said. “Accidents still happen. I’ve had many, many a burn. It’s just part and parcel of the job, especially when you’re forge welding, because you’ve got the metal so hot that it’s melting, and you’ve got to pound it together and sparks just fly. I routinely get what I call ‘pepper burns.’ I don’t like wearing shirts with sleeves because they’re restrictive, so my arms usually get covered in pepper burns because of the sparks.”
Olson is committed to forging as safely as possible, including always wearing safety goggles and wearing earplugs to protect her hearing whenever she’s not demonstrating. She also keeps her waist-length hair braided back and away from any heat sources.
“When I’m working, I don’t have hair on my hands,” she said. “I’ve lost my eyelashes and eyebrows before, just from the wind blowing the heat straight into my face. I’ll think, ‘Oh, what’s that smell?’ It’s my eyelashes burning.”
Growing in her craft
According to Olson, she learned much of her craft from her father, helping him with many of his commissions. She also studied under other blacksmiths, mostly colleagues of her father’s. She said she considers herself a “journeyman,” not a master blacksmith, since there is still more for her to learn.
“It’s a lifelong learning process, it really is,” she said. “There are times where I pick something up and go, ‘What if I try it this way? I’ve never done it that way.’ It’s not something that you’re ever going to learn enough about.”
Olson uses only coal for her forge, ordering bituminous blacksmith-quality coal from Iowa. She said this type of coal burns hotter and cleaner, allowing her to heat the center of her forge to more than 2,000 degrees Fahrenheit—the melting temperature of much of the metal she uses. She tends to work with cold rolled steel, buying it at Minnesota Iron & Metal Company in Mankato.
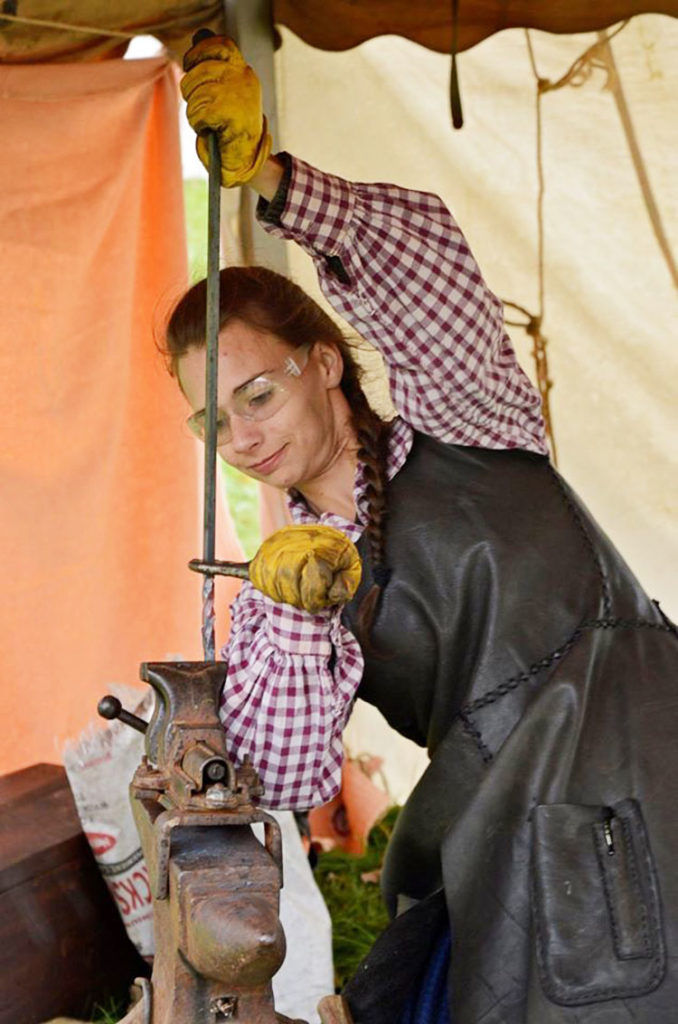
“I think one of the reasons that I like metal so much is you tell it what to do,” she mused. “Granted, you have to learn how to convince it to do what you want. I’m not a wood worker, but my husband does wood, and it seems like wood tells you what to do. You can’t just take a chunk of wood and do anything you want to. You have to follow certain lines in the grain of the wood. Once you cut, you can’t refill it. I could always weld something back together if I really needed to. There’s lot of ways to get around messing up with metal.”
Olson added that she takes commissions occasionally, but the project has to really interest her. Otherwise, she mostly enjoys playing around with metals herself as she learns new techniques and tries to create new items. She has crafted everything from tent pegs to knives, horseshoes to chandeliers. Some items, such as tent pegs, only take about three minutes, while she can spend days working on other projects. Her favorite thing she’s made is a set of six iron roses. The roses are about a foot long from stem to the tip of the rose, and they each weigh about 15 pounds.
“Each petal is hand crafted,” she said, “and everything is welded together on the leaves. I never sold them. It took so much time, you couldn’t put a price tag on them.”
Living history
Perhaps one of the most interesting parts of Olson work are the tools that she uses. She makes an effort to use period-appropriate tools, mainly from the Civil War era, and is currently working on building a new forge totally by hand, using traditional methods. She explained that the forge will be a replica of a Civil War era pack forge, and she designed it herself—even down to the number of rivets she needs to make by hand—after pouring over pictures of real-life war forges.
“I just thought it looked kind of cool,” she said about why she chose that style, “and it’s a challenge. I’d like to be able to say I made my forge myself.”
I think one of the reasons that I like metal so much is you tell it what to do. Granted, you have to learn how to convince it….
Olson said she hopes to finish the forge by this September. Once it’s done, it will weigh about 50 pounds—only half of what her current forge weighs.
“It’s definitely what I need for what I do,” she said. “My current forge weighs almost as much as I do… Most of my equipment weighs about what I do. I’ve worked my butt off for many years to be able to lift all this stuff, but I really can’t be handling such big equipment. I need a forge small enough that I can transport in my little truck.”
Teaching others
Besides working as a blacksmith, Olson also gives presentations on traditional blacksmithing practices from early American history. She dresses in handmade period-appropriate clothing (except for the safety goggles) and talks about how blacksmithing has changed throughout the years. Her first ever paid gig was when she was 15, when she was hired to give a presentation on blacksmithing at the Janesville Sesquicentennial.
“It was terrifying,” she admitted with a smile. “I still was working on public speaking, and I had to come up with my own demonstration and make sure I kept things in the 15-20-minute time span for kids. That’s probably one of the hardest things, because if you let the kids, they’ll keep asking question after question.”
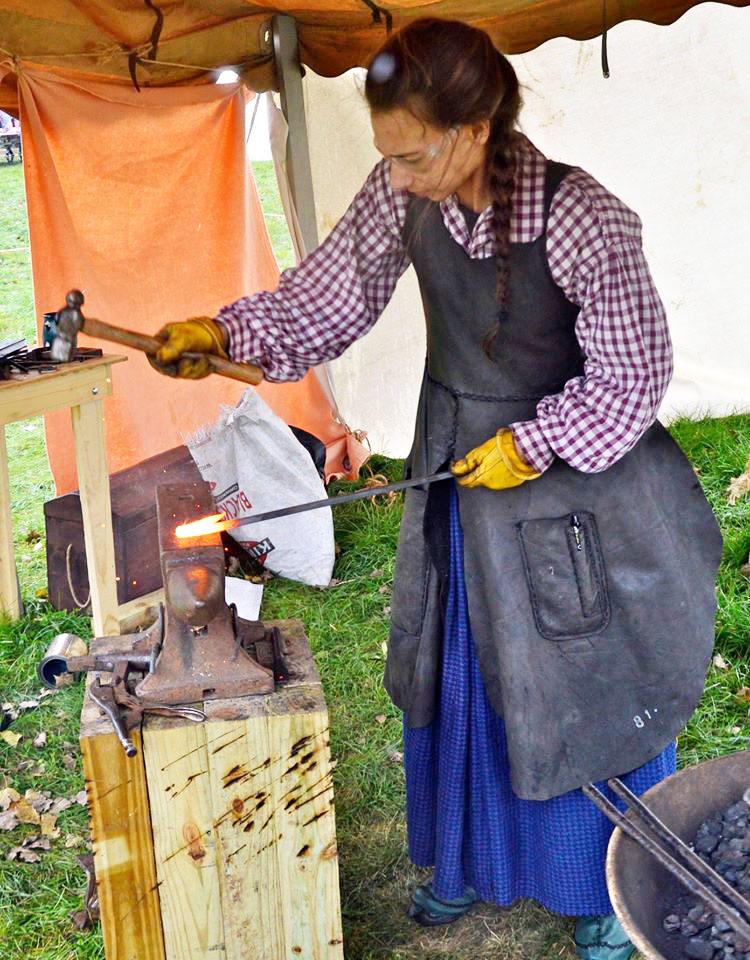
Throughout the years, Olson has continued to teach about her craft. During her demonstrations, she typically shares about the history of blacksmithing, women in blacksmithing, different techniques and other information, allowing for questions at the end. All the while, she demonstrates how to make items such as S-hooks, which take about 15 minutes to finish and include several techniques that she can demonstrate.
“When I put the twist in the metal, I heat the metal up and clamp it and twist it around,” she explained. “You can see it twist, and the kids always think that’s the coolest thing to see. When I was at the Bloomington event, seeing all the little girls and watching their faces light up… They’d say, ‘I want to work with metal, I want to be a blacksmith.’ And it’s very interesting, in today’s society, they never even thought about that they could do it. I just love seeing the expressions on the kids’ faces.”
Pushing through
Olson faced a setback a few years ago when she injured her shoulder, which required her to take about four years off blacksmithing. She still gave historical presentations at events, using a different character: The Herb Wife. As the Herb Wife, she would share about how herbs in Minnesota were traditionally used for medicinal purposes.
“During the four years that I couldn’t blacksmith, I just filled notebook after notebook with different designs,” she recalled. “I like taking clay or Play-Doh and sculpting it into a piece of metal. Play-Doh’s great… I go through a lot of Play-Doh.”
She was able to start giving demonstrations again two years ago. Even now, she says her shoulder is “temperamental,” so she uses a sports band to brace it, as well as wearing a special corset she designed herself to give her body more stability as she works.
“That’s a reason I have to make my equipment as light as possible, so I can do what I want to do,” she explained. “Even though I have some physical problems, I’m never going to stop blacksmithing.”
Last year, Olson gave four blacksmithing demonstrations at different events—the most she had done in recent years. She said she has three lined up for 2020: River Rendezvous in Bloomington in September, Big Island Rendezvous in Albert Lea in October and Mankato’s History Fest, also in October.
Additional Links
Windy Hills Creations by Takara Olson on Facebook
Getting to Know You
Who: Takara Olson
From: Denver, Colorado
Lives in: Nicollet, Minnesota
Family: Husband Josh, son Valin (10), daughter Athea (6) and daughter Mirabelle (4)
Dream project: Acid etching on knives. “I’ve wanted to ever since I came across a chapter on it from my dad’s books when I was 12. I’m waiting until my shoulder can withstand more pounding. I want to do it for me, and to learn. The more I learn, the happier I am.”
What she does when she’s not blacksmithing: She takes commissions to sew historical costumes, using traditional methods and materials, as well as custom-designed patterns. One gown based on 1740s fashions required 160 hours of embroidery work alone. Her goal is to create a costume from every period in history.
Fun fact: Olson participated in last year’s Minnesota River Builders Association Raw Fusion Fashion event in Mankato, designing and modeling her own costume. She has been invited to participate again at this year’s event, which will take place on May 8.
Contact info: takaramr@outlook.com
Female Blacksmiths in History
While blacksmithing has traditionally been seen as a predominantly male profession, Olson said there have been a surprisingly high number of female blacksmiths throughout the years—they just aren’t mentioned in history books that often.
“In a way, a woman’s role in history is not exactly what the history books say,” she said. “Women did everything and anything, mostly out of necessity. The first person to get drafted in the wars was a blacksmith and all his apprentices. Just because there was a war going on somewhere didn’t mean life at home stopped. So the women closest to the blacksmith would pick it up, whether or not they were ever actually exposed to it. Whether they’d ever picked up a hammer and participated in the blacksmithing, that’s totally irrelevant. People needed things done. Life continued, so the women closest to it continued it.”
Olson added that she has met a handful of other female blacksmiths throughout the years, though she still stands out for one interesting reason: at 5’3 and only 110 pounds, she tends to be the smallest blacksmith at any event.
“I wouldn’t say I’m one of a kind, because I have met other female blacksmiths,” she said, “but I’ve never met anyone as short as me.”
Appreciating history
Olson’s father was something of a collector when it came to forges and anvils, and Olson also developed a love for collecting blacksmiths’ tools. She has four forges and five anvils in her shop at the moment, including a 300-pound shop anvil that was given to her by her grandfather.
Olson is currently using her great-grandfather Earl Hunter’s forge, because hers died a few years ago after it developed a crack that was too large to fix. She estimates that the forge is about 150 years old. Meanwhile, she has an anvil that she inherited from her mother’s side of the family that is nearly 400 years old.
“There are certain things that I have that I’d never part with, not for a million dollars, because the history involved in them is amazing,” she said. “Most people don’t understand the value and the history involved in these incredibly old, beautiful antiques that are still perfectly usable. Anvils can get dinged up, dented, rusty… you just have to grind them down so they’re a nice flat surface with sharp edges. You just keep grinding them down. Considering how solid an anvil is, you’ve got a long way to go.”